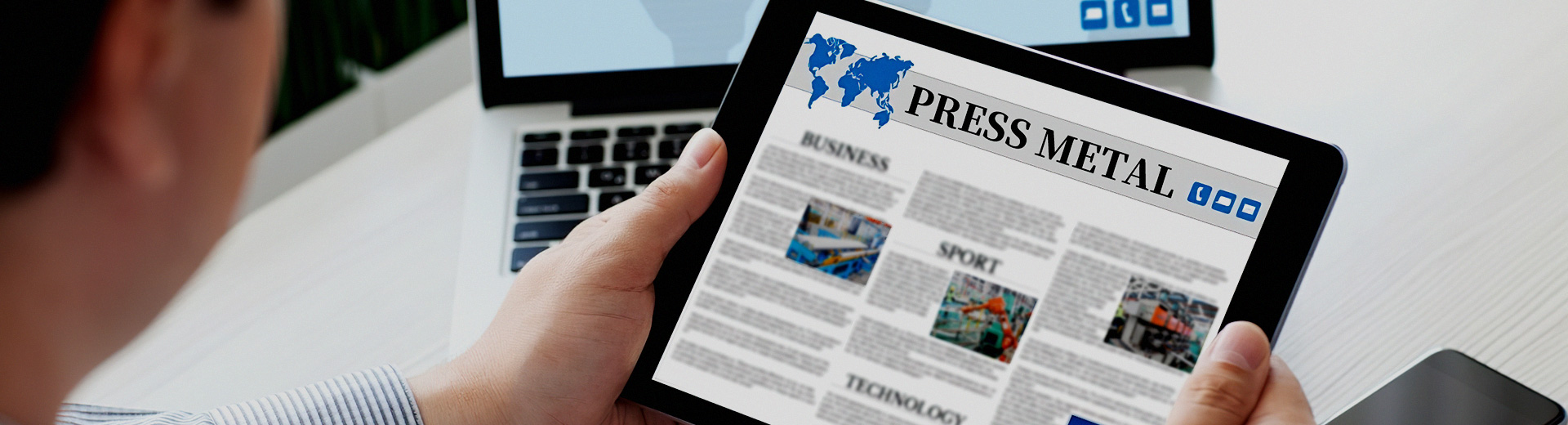
汽车发动机凸轮轴是发动机的心脏,而与凸轮轴联接的齿轮是否能与凸轮轴同步运转,决定了能否保证发动机动力的正常传输,这就要求齿轮与凸轮轴一定要保证高的联接强度。因此,只依靠高强度螺栓来紧固是不够的,现有设计中,往往采用弹簧垫片来增加轴与齿、螺栓与轴、齿之间联接强度。
目前汽车的轻量化设计理念,使得发动机的设计更为紧凑,凸轮轴的直径也更小,受到这种结构条件的限制,要保证齿轮与发动机凸轮轴的同步转动,即保证齿轮不丢转,从而确保发动机动力的正常传输,就需要凸轮轴与齿轮之间、螺栓与轴、齿之间的弹簧垫片具有更高的摩擦系数,以增加两个零件接触面的摩擦力。本发明提出的“一种金刚石化学复合镀汽车摩擦垫片的制备方法”就是用于加强汽车传动系统中齿轮与轴、齿与齿等高强度联接的高性能摩擦垫片,采用金刚石化学复合镀技术制造汽车摩擦垫片的方法还未见报导。
本发明的目的是克服现有弹簧垫片摩擦系数低,汽车凸轮轴与齿轮、齿轮与齿轮间等紧固强度不足的问题,而提供一种金刚石化学复合镀汽车摩擦垫片的生产方法,该方法生产的汽车摩擦垫片可实现高强度联接。本发明之方法是在薄弹簧钢质垫片上化学复合镀覆Ni-P-微米金刚石镀层,然后经150°C 350°C的热处理。所述的化学复合镀覆采用二步法镀覆,第一步镀覆一层5 15 U m厚度的Ni-P层;第二步镀覆Ni-P-微米金刚石镀层,该镀层厚度为所述金刚石粒径的一半,镀覆后金刚石嵌入镀层中呈半裸状态,金刚石的粒径为微米级,粒径为5 20 y m,Ni-P-微米金刚石复合镀层中,金刚石在镀层表面的体积百分含量为10 20%。本发明的有益效果薄质弹簧垫片通过化学镀覆Ni-P-微米金刚石镀层及随后的热处理,获得了具有高硬度、均匀分布的金刚石微粒的复合镀层,且金刚石嵌入镀层中呈半裸状态。当这种摩擦垫片置于凸轮轴与齿轮、齿轮与齿轮、螺栓与轴之间时,摩擦垫片上的金刚石微粒将自动嵌入相对面中,形成微型互锁,从而增强摩擦力,提高联接强度。因此,与普通弹簧垫片相比,这种金刚石化学复合镀汽车摩擦垫片不仅摩擦系数高,而且联接强度大。化学镀无污染、无毒无味、无三废排放,对环境保护非常有利,镀层不受基材形状的影响,可在材料的各部位均匀沉积,镀层硬度高,且镀层非常致密。
图I是金刚石化学复合镀汽车摩擦垫片结构示意图。图2是摩擦垫片工作状态下金刚石嵌合示意图。图3是金刚石颗粒扫描电镜形貌。图4是化学复合镀层表面扫描电镜形貌。图5是化学复合镀及150°C热处理后镀层表面形貌。图6是25 iim厚复合镀层断面的扫描电镜形貌。图7是12 iim厚复合镀层断面扫描电镜形貌。 图8是两面均有镀覆层的摩擦垫片断面扫描电镜形貌。图9是镀层X-射线是金刚石的添加量与镀层中金刚石含量的关系曲线。
具体实施例方式本发明之方法是在薄弹簧钢质垫片上化学复合镀覆Ni-P-微米金刚石镀层,然后经150°C 350°C的热处理;采用二步法镀覆,第一步镀覆一层5 15iim厚度的Ni-P层;第二步镀覆Ni-P-微米金刚石镀层,该镀层厚度为所述金刚石粒径的一半,镀覆后金刚石嵌入镀层中呈半裸状态,金刚石的粒径为微米级,粒径为5 20i!m,在Ni-P-微米金刚石镀层中,金刚石在镀层表面的体积百分含量为10 20%。如图I所示,为本发明之方法生产的金刚石化学复合镀汽车摩擦垫片结构示意图,该摩擦垫片由钢基体I和Ni-P-微米金刚石复合镀层2组成。图2是摩擦垫片工作状态下金刚石嵌合示意图,镀覆后金刚石嵌入镀层中呈半裸状态,当这种摩擦垫片置于凸轮轴与齿轮、齿轮与齿轮、螺栓与轴之间时,摩擦垫片上的金刚石微粒将自动嵌入相对面中,形成微型互锁,从而增强摩擦力,提高联接强度。如图3所示,是本发明所采用的金刚石颗粒扫描电镜形貌照片,金刚石粒径为10 15iim。镀覆前金刚石粉加入到乙醇中,放到超声清洗器中超声分散15-20min。图4为化学复合镀层表面扫描电镜形貌;如图4所示,金刚石颗粒均匀镀覆在钢基体表面,金刚石颗粒呈半裸状态,其中金刚石粒径为10 ym。采用二步法镀覆,第一步镀覆一层5 15 ii m厚度的Ni-P层,第二步镀覆Ni-P-微米金刚石镀层,该镀层厚度为所金刚石粒径的一半,镀覆后金刚石嵌入镀层中呈半裸状态,金刚石在镀层表面的体积百分含量为20%。图5是化学复合镀及150°C热处理后镀层表面形貌。从图5中可见,Ni-P-金刚石镀层热处理后,镀层还保持非晶组织状态,镶嵌在镀层中的金刚石颗粒没发生变化。金刚石粒径为5 10iim,在镀层表面的体积百分含量为10%。图6是25 iim厚复合镀层断面的扫描电镜形貌。由图6可见,镀层致密,与基体结合良好。图7为镀覆厚度为12 的镀层断面扫描电镜形貌。由图7可见,镀覆层非常均匀、致密。图8为两面均有镀覆层的摩擦垫片断面扫描电镜形貌。由图8可见,两侧镀层厚度非常均匀,镀层与钢基体之间结合得非常好。施镀前,钢基体经过活化处理之后,基体表面在微观状态下还是呈现凹凸不平,所以在镀层与基体的界面结合处,一些区域的镀层显得不平整,但是,随着Ni-P-金刚石的不断沉积,镀层不断加厚,镀层外表面也逐渐变得均匀平整。先进行20分钟Ni-P化学镀然后加入金刚石粉均匀搅拌,施镀时间为10分钟。图9是镀层X-射线可见,镀层的主要物相为Ni及金刚石,Ni的衍射峰呈现宽化,说明Ni-P-金刚石复合镀层基体还保持非晶态结构,金刚石沉积在Ni基体中,这与扫描分析结果是一致的。图10是金刚石的添加量与镀层中金刚石含量的关系曲线可见,镀液中金刚石的添加量对镀层中沉积的金刚石含量有很大的影响。即随着镀液中金刚石添加量的增力口,镀层中沉积的金刚石含量也增加,在金刚石添加量为8g/L的时侯,沉积的金刚石颗粒达到镀层总表面积的20%左右,可见镀液中金刚石添加量过低不利于形成一定含量的金刚石复合镀层,但是如果添加过多的金刚石则有可能造成镀液分散,不利于镀覆。所以,尽管金刚石的添加量几乎不影响镍与磷的沉积速度,但是考虑到为了不造成镀液分散,最终 镀层中获得10-20%的金刚石是较为贴切的。
1.一种金刚石化学复合镀汽车摩擦垫片的生产方法,该方法是在薄弹簧钢质垫片上化学复合镀覆Ni-P-微米金刚石镀层,然后经150°C 350°C的热处理。
2.根据权利要求I所述的一种金刚石化学复合镀汽车摩擦垫片的生产方法,其特征是所述的化学复合镀覆采用二步法镀覆,第一步镀覆一层5 15 y m厚度的Ni-P层;第二步镀覆Ni-P-微米金刚石镀层,该镀层厚度为所述金刚石粒径的一半,镀覆后金刚石嵌入镀层中呈半裸状态。
3.根据权利要求I或2所述的一种金刚石化学复合镀汽车摩擦垫片的生产方法,其特征是所述的Ni-P-微米金刚石镀层中,所述金刚石的粒径为5 20 y m。
4.根据权利要求I或2所述的一种金刚石化学复合镀汽车摩擦垫片的生产方法,其特征是所述的Ni-P-微米金刚石镀层中,金刚石在镀层表面的体积百分含量 为1(T20%。
本发明公开了一种金刚石化学复合镀汽车摩擦垫片的生产方法,该方法是在薄弹簧钢质垫片上化学复合镀覆Ni-P-微米金刚石镀层,接着进行150℃~350℃的热处理;采用二步施镀法,第一步,在钢垫片上镀覆一层Ni-P层,第二步,在Ni-P镀层上继续镀覆Ni-P-微米金刚石镀层,镀层中的金刚石呈半裸状态;工作状态下,镀层中的金刚石微粒自动嵌入相对面中,形成微型互锁,从而增大摩擦力,实现高强度联接;该摩擦垫片可应用于汽车发动机传动系统中,它可以联接齿轮-齿轮、齿轮-链轮、齿轮-轴等,保证轮与轴等保持同步运转,对高功率、大扭矩的输出起着重要的作用。
如您需求助技术专家,请点此查看客服电线.探索新型氧化还原酶结构-功能关系,电催化反应机制 2.酶电催化导向的酶分子改造 3.纳米材料、生物功能多肽对酶-电极体系的影响4. 生物电化学传感和生物电合成体系的设计与应用。
1.高分子材料的共混与复合 2.涉及材料功能化及结构与性能的研究; 高分子热稳定剂的研发
1. 晶面可控氧化铝、碳基载体及催化剂等高性能、新结构催化材料研究 2. 乙烯环氧化催化剂的研究与开发 3. 低碳不饱和烯烃的选择性氧化催化剂及工业技术开发
1. 加氢精制 2. 选择加氢 3. 加氢脱氧 4. 介孔及介微孔分子筛合成及催化应用
一种基于屏蔽层化学取消自动化生产线的电镀磨粒工具分段电镀方法与制造工艺
具有密封的覆镀通孔的微机械部件和用来制造具有密封的覆镀通孔的微机械部件的方法